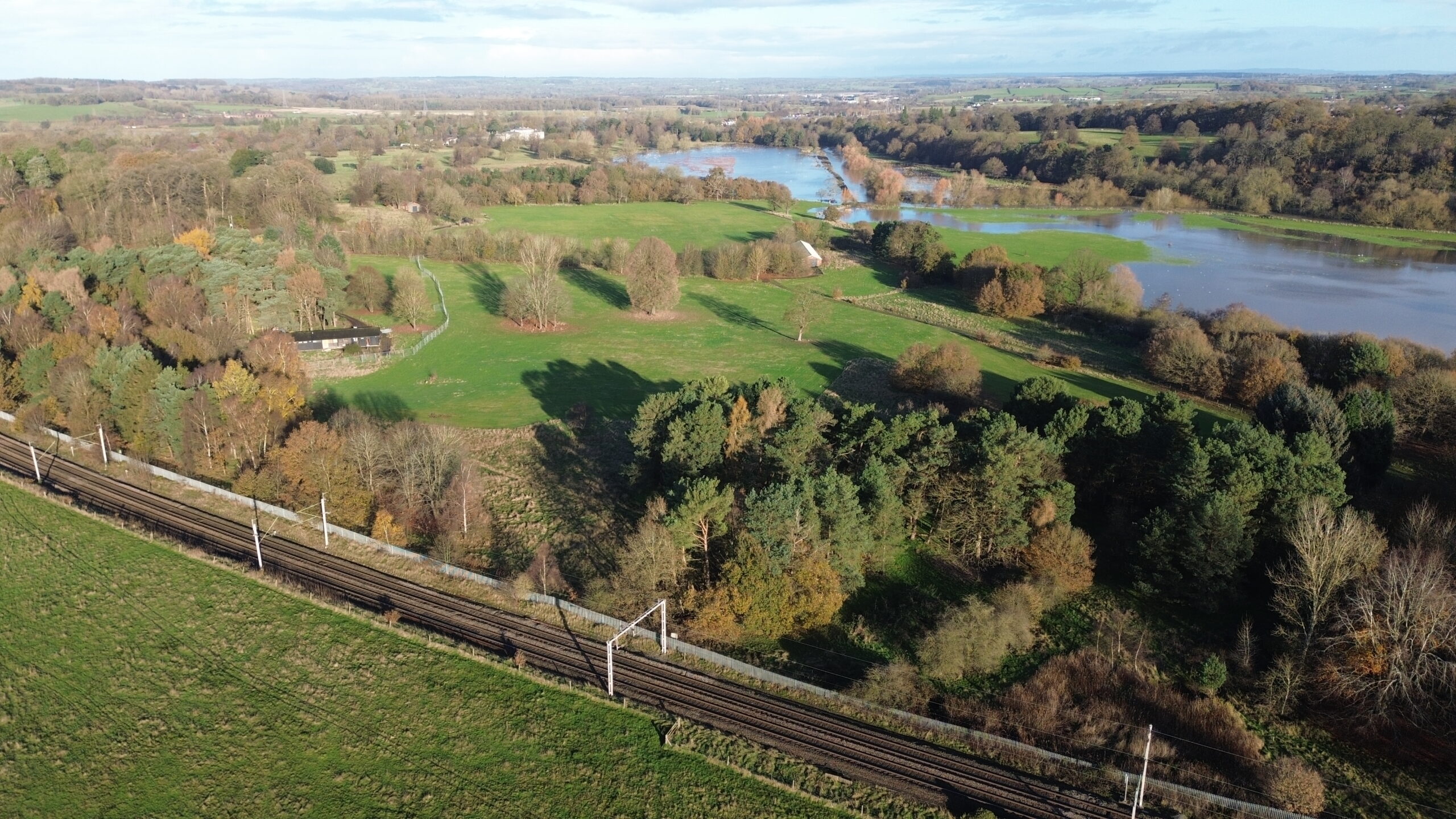
Prioritising sustainability and preserving history at Shugborough
Shugborough Estate, a historic National Trust property in Staffordshire, is undergoing a major development programme to cultivate and promote the site’s natural landscape and highlight its unique past.
On track for transformation
As part of the 57-week project, which kicked off in November 2024, we were instructed to deliver a series of reorientation works which would transform the site’s accessibility. This includes an additional car park, bridge, woodland paths, visitor centre and facilities.
We are also adding a new entrance and access road from the A513, a new exit road which includes a new bridge over the existing Sher Brook, and new pathways across the site. The works will improve access to the site, allowing visitors to easily enter and leave the historic estate through the woodland areas.
Our construction works are prioritising eco-friendly practices and sustainability, echoing the National Trust’s shared values, of driving sustainability and supporting local communities. For example, we’re using straw bales, UK-felled timber, lime, clay and other porous materials for buildings and tapping into solar energy with panels and lighting bollards to enable safe navigation for visitors during all hours of the day.
To maintain the integrity of Shugborough’s local flora, all plants are quarantined before being brought to site. By adopting a nature-first approach, we’re preserving the site’s woodlands and gardens for a future generation of visitors.
We have decades of experience combining excellence and practicality and are working closely with the National Trust team to create visually appealing spaces that can be enjoyed by the local community and visitors. In order to incorporate Staffordshire’s rich nature into the design, we will be building the new visitor centre around an ancient oak tree.
The right touch to improve accessibility
Improving access is a crucial part of this project and one of the estate’s key commitments, which makes this an exceptionally rewarding project for our specialist in-house team. From design to implementation, our expert team are experienced in providing the right touch to create accessible, dynamic spaces that meet a variety of needs.
Through collaborating with the National Trust team, our aim is to create a space that will serve a wide range of needs for visitors, the local community, and nature for years to come.
Find out more about how we transform sites when delivering civil engineering projects across the country.